Bentley includes 3D-printed gold in new Batur
Process is believed to be world-first in the industry.

Bentley has introduced a new 3D-printed gold process to its upcoming Batur.
In what is believed to be a first for the automotive industry, the process sees Bentley’s ‘additive manufacturing’ technique add 210 grams of 18-carat yellow gold to the coupe.
This 3D-printed gold is applied to areas such as the dial which encircles the start-stop engine button, the organ stop ventilation controls on the dashboard as well as a small section on the steering wheel.
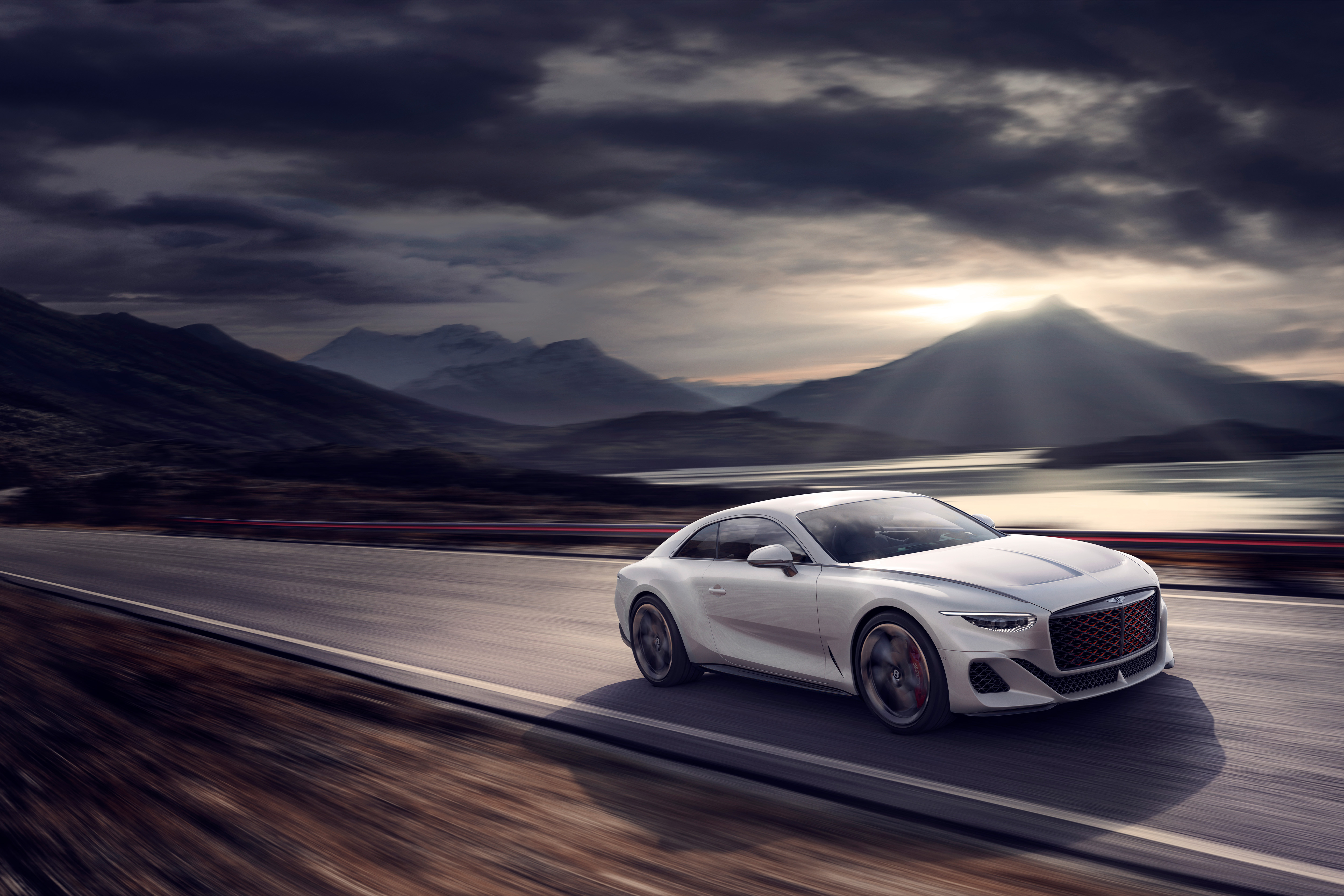
All of the gold used is 100 per cent recycled from old jewellery. It’s then ground into a fine powder, which is required for the 3D printing process. Each part is created using computer aided design (CAD) models, before the component is printed using laser melting printers. Each piece is then finished by professional jewellers using traditional polishing techniques.
Dr. Matthias Rabe, member of the board for research and development at Bentley Motors, said: “Bentley’s approach to additive manufacturing is industry leading, evident through our pioneering use of a luxury metal in the design and development process of the Batur. One of the key benefits is that it is efficiency led, cutting down on the cost and complexity of a myriad of jobs but maintaining the value of a rare resource.
“As Bentley embraces an exciting future, we see huge potential in advanced, innovative technologies. Processes such as 3D printed gold will be a springboard that allows our customers an even greater ability to personalise, further enhancing the individualisation programme offered on every car.”
Each part created is hallmarked in Birmingham’s Jewellery Quarter as a sign of authenticity.